Эпоха возрождения давно прошла, но герой этого кейса, Андрей Шилейко, удачно бы вписался в нее на 100%. Добродетели тех времен, разносторонние интересы и постоянное развитие личных навыков - это как раз про него.
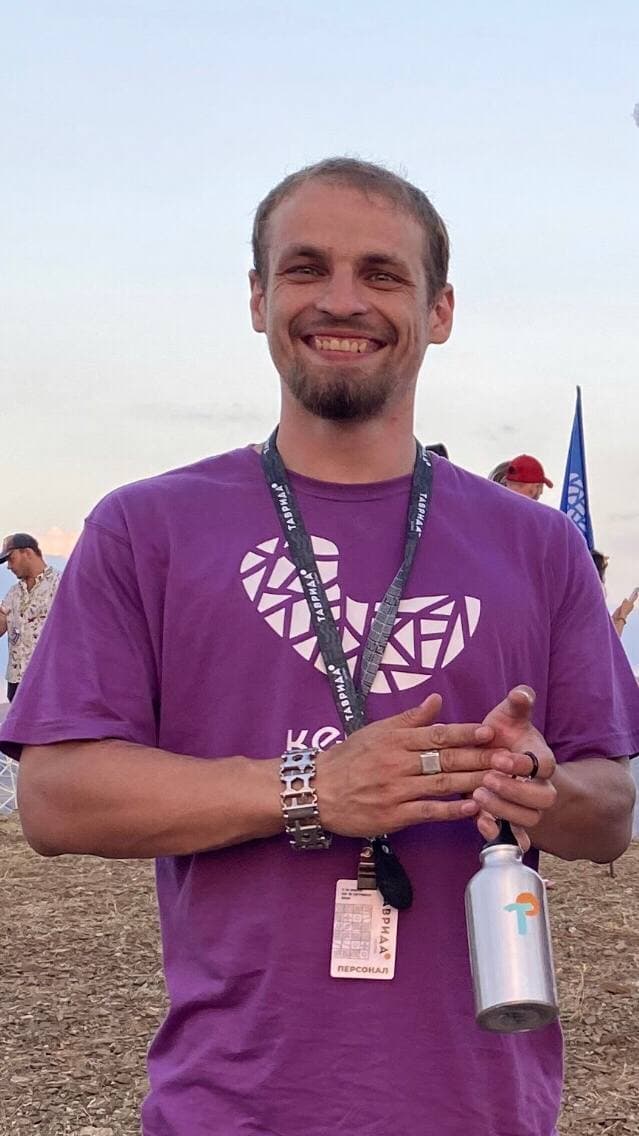
Андрей Шилейко
Два диплома Российского технологического университета МИРЭА по сварочному делу и аддитивным технологиям в машиностроении удачно сочетаются с созданием арт-объектов для Burning man 2019, работой в мастерской для киношников «Maddragon» и десятком других направлений. «Физик» и «лирик» в одном лице.
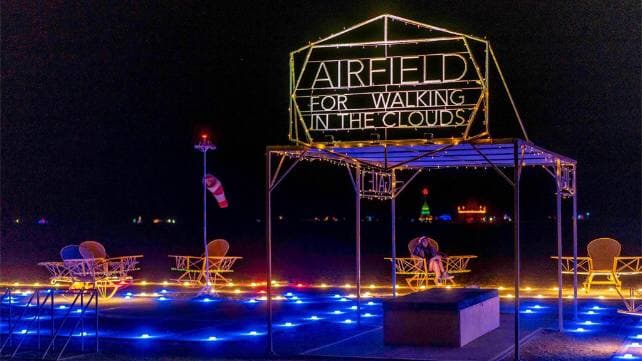
Арт-объект для Burning man 2019. «Аэродром для витания в облаках» . Фото предоставлено Андреем Шилейко
Для справки: Burning man - ежегодное культурное событие. Проходит в пустыне Блэк-Рок в Неваде (США). Глобальная арт-площадка для костюмированных шествий, показа инсталляций современного искусства, музыкальных выступлений.
Первым шагом к аддитивным технологиям стала покупка китайского 3D принтера в 2019 году, причем Андрей как истинный «технарь» сразу же поставил перед собой комплекс конкретных задач:
- Понять основные принципы 3D печати;
- Освоить новое оборудование;
- Обозначить плюсы и минусы принтера;
- Определить точки роста в нише аддитивных технологий.
В быстром освоении нового направления помогло высшее образование по сварочным технологиям. В чем взаимосвязь?
«Если приходится объяснять кому-то про 3D печать обычно провожу аналогию со сваркой, потому как если к сварке добавить еще одну координату, то получится именно 3D печать. Такое как раз и практиковалось только это называли наплавкой. Имея хороший опыт в этой сфере, довольно часто провожу аналогии по тому, как регулируются различные стандарты и как можно классифицировать, например дефекты в 3D печати.»Андрей Шилейко
После активной эксплуатации «бюджетника» стало понятно, что нужно более мощное и совершенное оборудование. Осознанный выбор пал на Hercules 18, так как в нем был необходимый функционал. Тем более появилась возможность приобретения его по подписке.
Большим подспорьем было содействие ИМПРИНТА в корректировке прошивки ПО принтера для печати на высоких температурах, так как предстояла работа с композитными материалами.
Как водится, первые клиенты в большинстве случаев - это знакомые. «Пробой пера» стала печать розеток для мебели, но особых затруднений она не вызвала.
Как ни странно ожидаемый «первый блин» «вылез» во втором заказе ( кронштейны для боковых зеркал автомашины Ока), который стал «сериалом с продолжением». Ибо изначально неудачный выбор материала PLA привел к разрушению первого комплекта деталей. И лишь со второй попытки все получилось как надо.
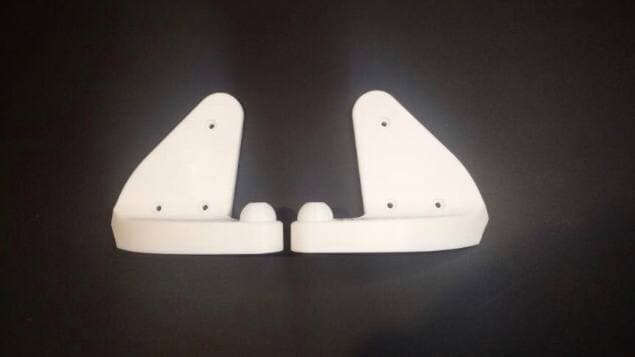
Кронштейны для боковых зеркал автомобиля Ока. Материал: Eternal (ASA) от REC. Принтер Hercules 18. Время печати 35 часов. Температура сопла 245 °С. Температура стола 110 °С. Фото предоставлено Андреем Шилейко
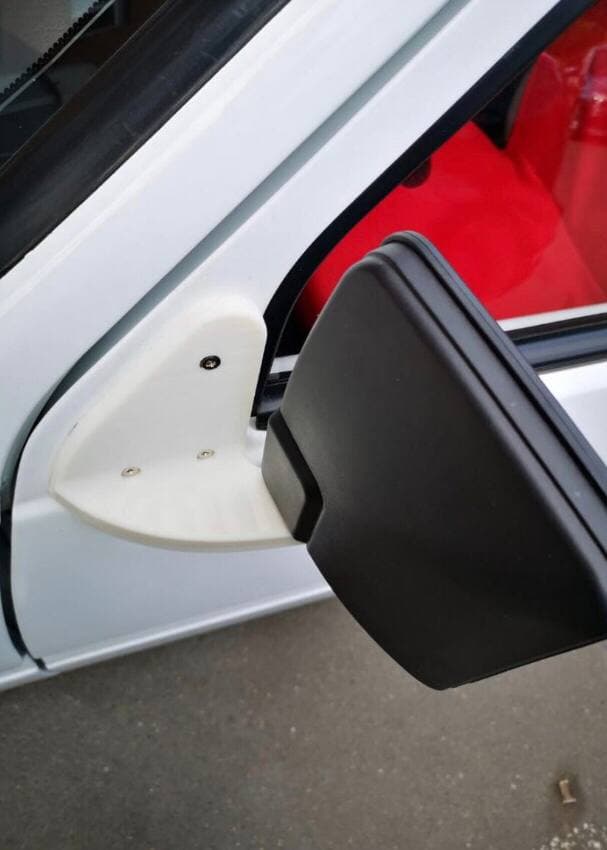
Кронштейны для боковых зеркал установлены на автомобиле Ока. Фото предоставлено Андреем Шилейко
В целом специфика заказов, с которыми обычно приходят клиенты (небольшие мастерские) - невозможность приобретения деталей изготовленных традиционным способом:
- Либо их не выпускают отдельно в принципе;
- Или себестоимость заказа у производителя гораздо выше, чем печать на 3D принтере.
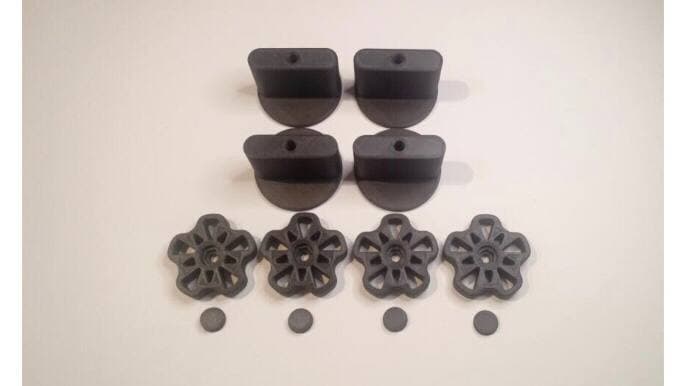
Крепления для топливного бака моторной лодки. Материал: TOTAL CF-5 от Filamentarno. Принтер Hercules 18. Фото предоставлено Андреем Шилейко
Показательным примером второй причины было задание по массовому изготовлению пластиковых элементов. Оригиналы производят в Испании, что с учетом курса Евро и кризиса в экономике сделало аддитивные технологии палочкой-выручалочкой конкретно в этом случае.
Всего нужно было напечатать 350 (!) комплектов с полным совпадением по цвету и прочностным характеристикам. Опыт Андрея плюс высокая производительность принтера Hercules 18 помогли с честью выполнить обязательства.
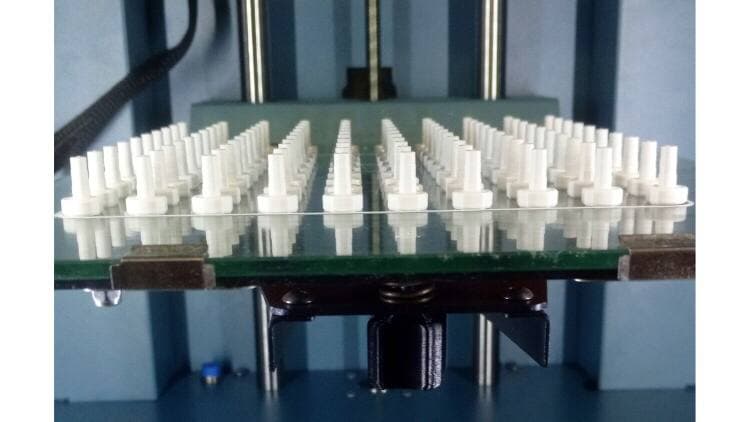
Пластиковые элементы. Материал: ASB от BestFilament. Принтер Hercules 18. Фото предоставлено Андреем Шилейко
Впрочем, и это не потолок. Следующий заказ - на 2 550 штук был также исполнен вовремя.

Пластиковые элементы. Партия: 2 550 штук. Материал: PLA от BestFilament. Принтер Hercules 18. Фото предоставлено Андреем Шилейко
Однако аддитивные технологии сейчас - это не только про сувениры и прочую мелочевку. Особая гордость - изготовление деталей для оборудования, работающего с металлом. Сами понимаете, что нагрузки, к примеру, на вальцы трубогибочного станка или гибочную оснастку серьезные. 3D печать таких деталей оптимальна для производственных партии до 10 000 единиц готовых изделий и позволяют:
- Разработать уникальную оснастку в очень сжатые сроки и обойтись без подрядчиков;
- Оптимизировать расходы на изготовление оснастки;
- Уменьшить себестоимость для небольших партий изделий за счет отсутствия расходов на разработку, изготовление и доводку металлической оснастки.
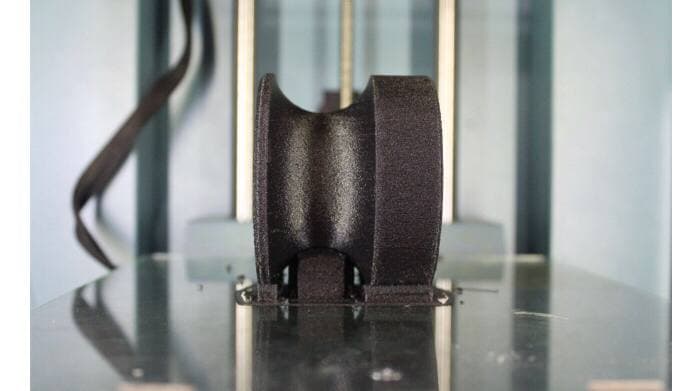
Валец для гибки труб диаметром 30х2 мм из алюминия. Материал: Titan GF-12 от «Filamentarno!». Принтер Hercules 18. Фото предоставлено Андреем Шилейко
Другой пример.
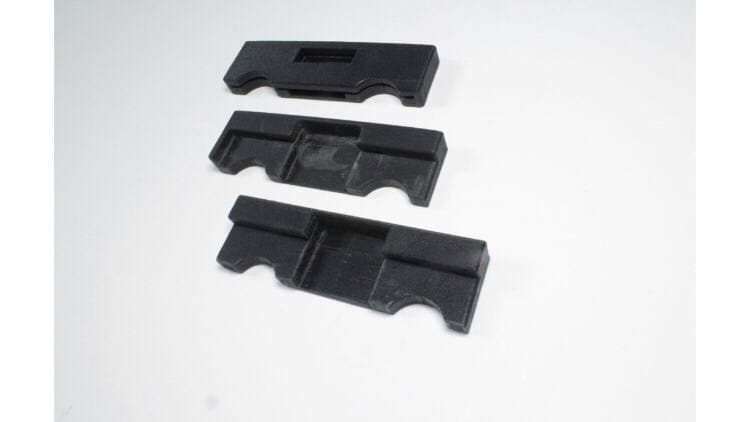
3 варианта оснастки для изготовления дверной планки. Изготовление и корректировка проведены в очень сжатые сроки. Фото предоставлено Андреем Шилейко
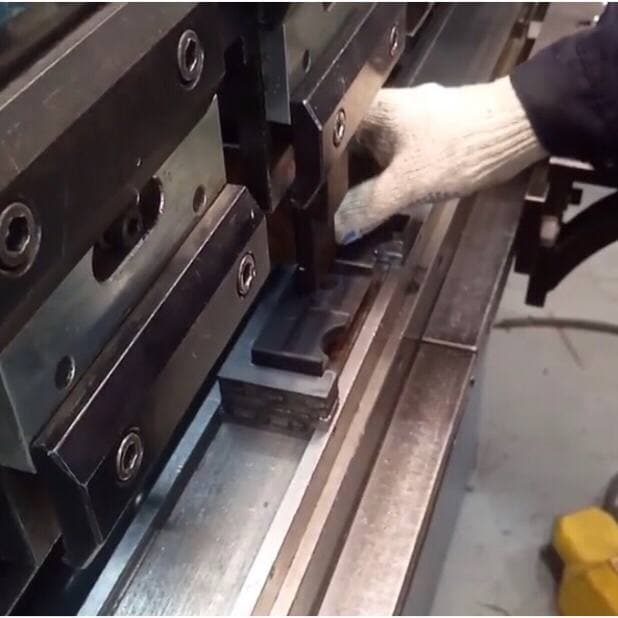
Оснастка для изготовления дверной планки. Материал: Titan GF-12 от «Filamentarno!»
Принтер Hercules 18. Фото предоставлено Андреем Шилейко
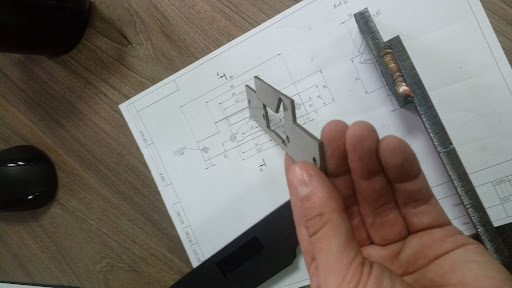
Дверная планка. Фото предоставлено Андреем Шилейко
«На прошлой неделе распечатал оснастку для гибки, тоже из Titan GF-12 и удалось согнуть 10 мм стальную пластину. У гибщика со стажем 20 лет были очень большие глаза что такое вообще возможно.»Андрей Шилейко
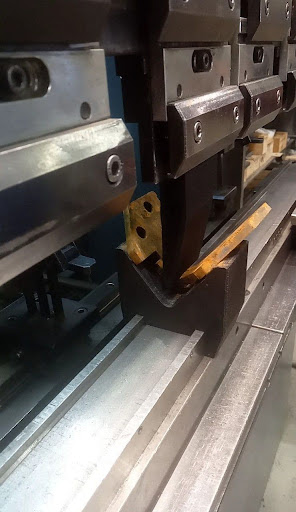
Пуансон и матрица для гибки 10 мм стали. Материал: Titan GF-12 от «Filamentarno!»
Принтер Hercules 18. Фото предоставлено Андреем Шилейко
И все же 3D печать деталей для Андрея - больше хобби, чем работа. Иногда даже приходиться отказывать клиентам из-за занятости в других проектах и научной работой (учеба в аспирантуре обязывает).
В настоящее время ему как аспиранту и инженеру-технологу более интересно применение аддитивных технологий как части комплексного решения при разработке сложных технических проектов.
Хорошим примером такой деятельности является сборка в рамках открытого проекта MPCNC универсальной платформы точного управления движением под оборудование с ЧПУ (фрезерный станок, 3D-принтер, лазерный резак, виниловый резак, плазменный резак).
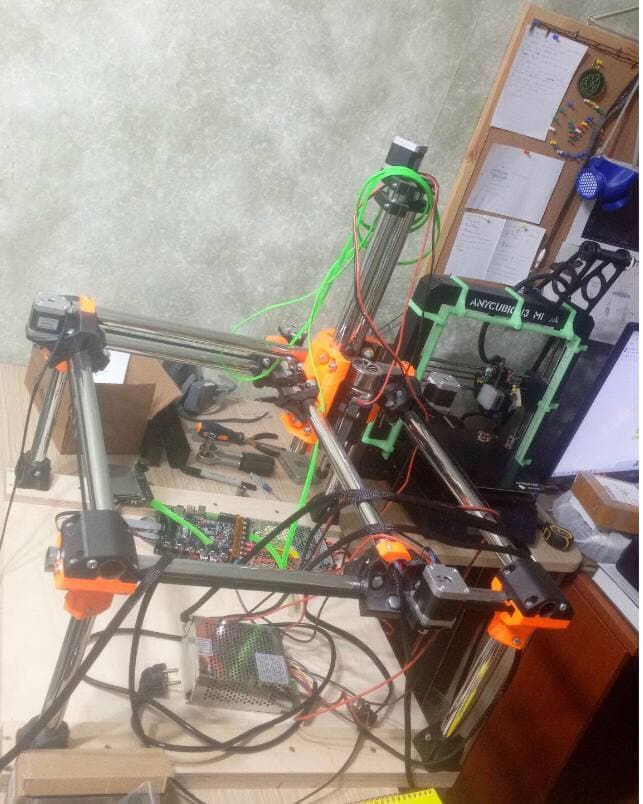
Универсальная платформа открытого проекта MPCNC. Материал пластиковых деталей: ABS GF-4 от «Filamentarno!». Время печати: 245 часов. Принтер Hercules 18. Фото предоставлено Андреем Шилейко
В ходе монтажа пригодился опыт в электронике, сборке механики, а уже после окончательной сборки платформы можно отработать навыки по фрезеровке, написанию управляющих программ. Не говоря о том, что все пластиковые элементы платформы были напечатаны на Hercules 18
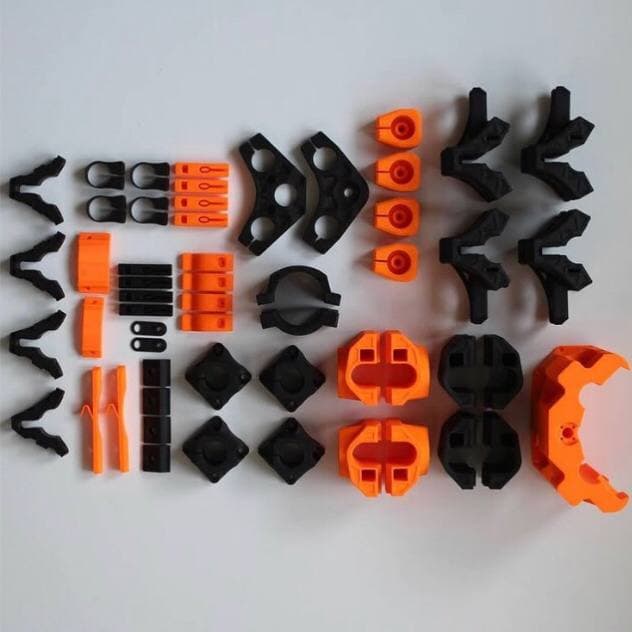
«Для меня 3D принтер такой же ЧПУ станок, как и остальные (токарный, фрезерный, гибочный, лазерного раскроя). Он может изготавливать, как и конечный продукт, так и «полуфабрикат», который будет частью чего-то большего. Для меня второй вариант более интересен, так при нем получаются более сложные и функциональные изделия.»Андрей Шилейко
Современные технологии помогают обозначить горизонт решений, а заодно и выявляют точки соприкосновения со смежными областями. Та же 3D печать, по словам молодого ученого, не только поле исследований расходных материалов и оборудования, но и способ узнать ответы на чисто прикладные вопросы. Например, подходят ли изделия, распечатанные на 3D принтере, для применения в металлообработке и множество других сфер.
Наглядным примером такого подхода стала работа над диссертацией в магистратуре. Тема - Изменение прочностных характеристик материала в зависимости от параметров печати. Это стало серьезным вызовом и потребовало мобилизации ранее накопленного опыта.
В ходе научного обоснования пришлось:
- Изучить большой объем материалов по испытаниям полимеров;
- Придумать регламент испытаний;
- Распечатать тестовые образцы - 72 лопатки;
- Провести испытания на разрывной машине - 8 часов;
- Самостоятельно обработать результаты.
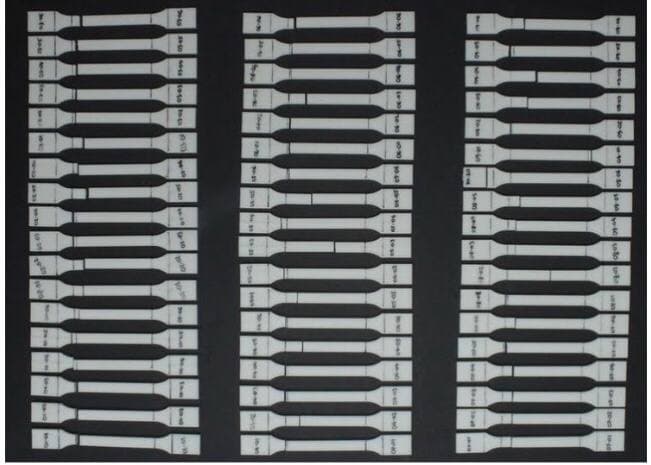
Итогом кропотливой работы стал график, где отразилась зависимость прочностных характеристик образцов от температуры печати.
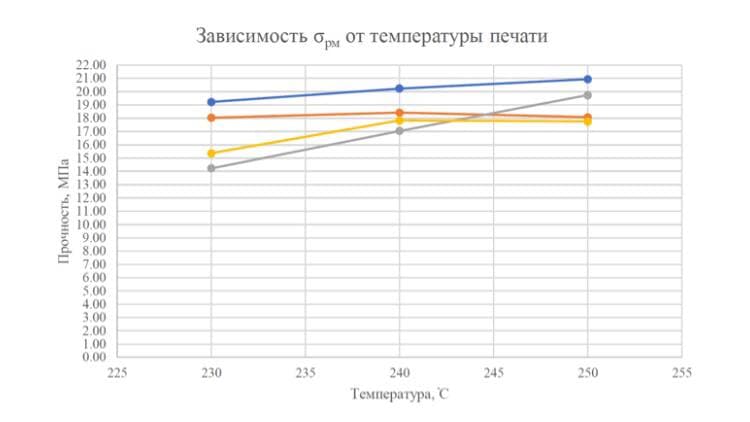
В планах на будущее у Андрея научные исследования по возможности совмещения 3D печати и гибки металлов. Для этого понадобится проведение испытаний, многочисленные исследования и подбор наиболее подходящих материалов для таких операций. Сейчас все подчинено проработке мероприятий в этой области.
А помимо этого погружение в тему литья, написание программ для фрезеровки, создание арт-объектов. Как видите, между отдыхом и работой очень тонкая грань и 3D печать - универсальная технология как для первого, так и для второго.